services
hHVAC VALIDATIONS
Clean Room
/ Area Validation
Clean Room
/ Area Validation
Vashishta engineering ServicesPrivate
Limited is a leading specialist provider of validation services. We have grown
as a reputable company and offer our services nationally & internationally.
As an industry leader we are having more than 10 years / nearly a decade of
experience using both thermocouples and thermistors.
Cleanroom Validation/HVAC
Validation is performed for a variety of reasons. To ensure that the design of
the facility is fit for its intended purpose; to ensure that the facility,
equipment, and environment meets User Requirement Specifications (URS); to
ensure that the facility, equipment, and environment meet defined regulatory
requirements; to ensure that the facility, equipment, and its environment
function together as a system to meet defined standards.
We provide and extensive range
of services pertaining to clean room validation by our panel of expert
professionals available with us.
Vashishta engineering Servicesperforms
the HVAC validations as per ISO 14644-1,2,3, EU GMP/EC GMP, WHO-TRS-937,
WHO-TRS-961, Schedule M (National Regulatory Body) guidelines for all room
classifications.
Cleanroom Certification
validated cleanrooms are
validated to a required class of cleanliness. The level of cleanliness chosen
is driven by user requirements. Cleanroom classes are defined in ISO1464-1:
Monitor And Control
A constant monitoring program is
required after certification. Requirements for compliance are found in ISO
14644-2.
Statistical analysis for
cleanroom parameters is encouraged as a tool for monitoring the cleanroom after
certification to ensure compliance. The tool of choice is statistical process
control, SPC.
Methods for evaluation and
measurements for Certification are specified in ISO14644-3. It calls out for
the following ten tests.
·
Air flow Test & ACPH
Calculations
·
Installed Filter System Leakage
Test (using PAO)
·
Non-Viable Particle Count Test
·
Recovery Test
·
Air Flow Pattern Test (Using
Water Fogger)
·
Air Pressure Balancing
·
Containment test
·
Temperature & RH Measurement
·
Light Intensity Measurement
·
Sound Level Measurement
Once certified to a particular
class the cleanroom factors are monitored to ensure that parameters have not
drifted, or changed, and that the environment is under control.
Vashishta engineering Servicescarries
out following tests to validate clean rooms/clean zones.
Air flow Test & ACPH
Calculations
We conduct Air Velocity
Measurement / tests to determine the average filter face velocity and
uniformity, and the average room airflow velocity and uniformity within a clean
room. The average airflow velocity is calculated by dividing the total of the
airflow grid velocities by the number of readings taken. Air Exchange Rate
tests determine the total air volume get in to the room within a clean room.
The use of TSI Accubalance Air Capture Hoods of Model No.8375, assures accurate
test results. The hood measures air volume flowing through registers, diffusers
and grills. Weighing just 3.5 kgs, these air capture hoods are easy to use and
carry. These hoods simply hold the accubalance up to a diffuser or grill and
read direct supply or exhaust airflow on the large digital display.
Installed Filter System Leakage
Test (using PAO)
We conduct complete HEPA/ULPA
filter integrity testing services. These are offered for both the
Pharmaceutical and Microelectronics industries. All filter integrity tests
performed by us are executed in accordance with IES-RP-CC-001-86 & ISO
14644. We are equipped to perform HEPA Filter Integrity Test with both Di–Octal
Phthalate (DOP) and Poly Alpha Olefin (PAO) depending on client-facility's
specific requirements. The tests assure that client's filters are in
conformance with various standards and/or governing agency requirements.
Testing and evaluating filters minimum once annually and potentiality twice
annually is required for optimum performance. Proper documentation and
certification is provided by us and this also helps predict potential
performance issues and increases filter life.
Non-Viable Particle Count Test
We are Vashishta engineering
Servicesa reputed name in offering clean room validation services. Our Particle
Count Test provides complete airborne particle count cleanliness
classification. The test is performed to determine the actual particle count
level within the facility at the time of the test. The test identifies particle
count on basis of As-Built, At-Rest, or Operational as per ISO 14644 , EU GMP .
The particle size(s) of interest, the room occupancy state and the room
classification shall be known prior to the beginning of the tests and shall be
as specified in the URS documents.
Recovery Test
We execute recovery tests for
clients across Industries. These tests demonstrate the ability of the clean
room to remove particulate by purging the area with filtered air. It also
testifies if the room can change from a "dirty" to "clean"
state within the specified time. The test is conducted by experienced
technicians from team. Our technicians have enriching experience and provide
clients with high quality service. The ultimate goal of our company is to
assure complete satisfaction of clients through effective execution of services
and by providing best array of clean room equipment. We ensure that client's
clean room facility is performing properly and accurately.
Air Flow Pattern Test (Using
Water Fogger)
We offer Airflow Visualization
Test as a part of the validation process. Visualization is carried out by using
water fogger and taking Video Graph. The purpose of the airflow visualization
test is to show the actual airflow pattern throughout the unidirectional clean
room. The test can also be used to demonstrate the effects on airflow caused by
equipment. It is best to perform this test after all airflow velocity and
uniformity tests and room pressurization tests have been performed. The test
determining the airflow patterns within a room using ISO 14644 guides. This
visual monitoring service is important in:
Clean Room laminar flow tests
·
Airflow balancing
·
Fuming Hoods
·
Point Exhaust tests
·
Personnel safety exhausts
verification
·
Pressure balancing between rooms
and spaces
·
Leak detection in ducts
Air Pressure Balancing
We conduct Room Pressurization
Test for industrial clean rooms. As a part of the validation process, this test
verifies that a pressure differential meet the specified requirements.
Containment Test
We conduct Containment Tests for
client's clean room facility. The test is carried to demonstrate that airborne
contamination does not enter from a higher pressure area adjacent to the clean
room by means of leaks in the construction materials. The test is conducted by
trained and experienced technicians using modern instruments that assure
accurate results.
Temperature & RH Measurement
We conduct validation tests that
include Temperature and Humidity Measurements / Tests. Two levels of
temperature and humidity tests are used by us depending on the requirement. In
the first level, general temperature and humidity uniformity are tested. The
general level test is used to ensure that the clean room's HVAC system
maintains the specified levels of temperature and humidity required for
occupant comfort. The second level or the comprehensive level test identified
that the clean room HVAC systems needs to maintain the specified levels of
temperature and humidity required for both occupant comfort and process
temperature control.
Light Intensity Measurement
The purpose of the lighting
level tests is to verify that the installed light levels and uniformity meet
the specified requirements. We make use of modern testing instruments for
assessment of lighting lux levels and intensity.
Sound Level Measurement
We perform noise level test that
measure the sound pressure. The measurements will vary based on the occupancy
state-of-the-art clean room.
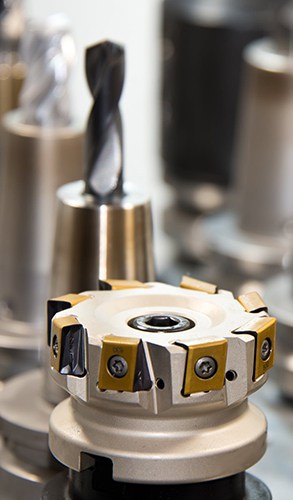
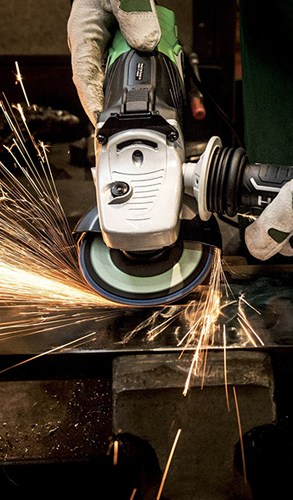
Our Innovations
Industry Focused Products!
Roller Chain Drives
Proin gravida nibh vel velit auctor aliquet. Aenean sollicitudin, lorem quis bibendum auctor, nisi elit consequat ipsum, nec sagittis sem nibh id elit. Duis sed odio sit amet nibh vulputate cursus a sit amet mauris. Morbi accumsan ipsum velit.
Inductive / Capacitive Sensors
Proin gravida nibh vel velit auctor aliquet. Aenean sollicitudin, lorem quis bibendum auctor, nisi elit consequat ipsum, nec sagittis sem nibh id elit. Duis sed odio sit amet nibh vulputate cursus a sit amet mauris. Morbi accumsan ipsum velit.
Motors & Gear Motors
Proin gravida nibh vel velit auctor aliquet. Aenean sollicitudin, lorem quis bibendum auctor, nisi elit consequat ipsum, nec sagittis sem nibh id elit. Duis sed odio sit amet nibh vulputate cursus a sit amet mauris. Morbi accumsan ipsum velit.
Conveyor Chains
Proin gravida nibh vel velit auctor aliquet. Aenean sollicitudin, lorem quis bibendum auctor, nisi elit consequat ipsum, nec sagittis sem nibh id elit. Duis sed odio sit amet nibh vulputate cursus a sit amet mauris. Morbi accumsan ipsum velit.